Friday, March 24, 2006
1. INTRODUCCIÓN.

Estos apuntes sobre el uso de barro y cerámica en construcción han sido redactados por los alumnos del Grupo J de la Escuela de Arquitectura de Madrid, como experiencia piloto de aprendizaje basado en herramientas web. La Profesora encargada del grupo es Dña. Soledad García Morales.
Como base de partida se han utilizado los apuntes editados por el Profesor D. Félix Lasheras Merino, de la Escuela Técnica Superior de Arqutectura de Madrid. Estoa apuntes han servido para elaborar un primer borrador y esquema de trabajo, que se ha enriquecido después con diferentes imágenes, textos y enlaces.
2. HISTORIA DEL USO CONSTRUCTIVO DEL BARRO Y LA CERÁMICA. EJEMPLOS DE EDIFICIOS SIGNIFICATIVOS
La arcilla como material constructivo era ya utilizado por las poblaciones de Mesopotamia hacia el 6000 a.C. El inicio de la construcción en materiales imperecederos se produce cuando el hombre abandona el nomadismo para adoptar unas pautas de vida sedentarias, así los hombres fueron construyendo con los materiales que les rodeaban.
En casi todas las construcciones se utilizaba la arcilla por ser el material más asequible. Su uso en la construcción se difundió primero a Egipto y al lejano Oriente, pasando después a Europa a través de Grecia y Roma.
Los primeros núcleos constructivos se dan en Mesopotamia en el IX milenio a. C. y eran casas rectangulares construidas en tapial. En el VII milenio a.C. se detectan en Mureybet viviendas edificadas con bloques calcáreos unidos por mortero de arcilla. En Ali Kosh aparecen los primeros ladrillos de adobe y se empieza a erigir edificios con ellos durante el periodo de Samarra (5500 a.C.) En el 3000 a.C. aparece el ladrillo cocido en el Palacio de Nippur en Mesopotamia usándose como elemento decorativo y cubrimiento de muros realizados en adobe. El ladrillo cocido suponía una gran mejora con respecto al de adobe por ser más duro además de resistir mejor al paso del tiempo y los agentes naturales.
Las sociedades afincadas entre el Tigres y el Eufrates lo emplearon para crear sus grandes ciudades fortificadas que estaban constituidas por casas particulares, palacios y los conocidos zigurats.
A Egipto llega más tarde y se empezarán a utilizar durante la Primera Dinastía (3050 a.C.) en las tumbas de Abidos. Su definitiva difusión tuvo lugar en el Imperio Nuevo (1540-1070 a.C.) y sobre todo en la época greco-romana. Durante este tiempo ambos tipos de ladrillo convivieron siendo muy habitual la utilización de ambos materiales en una misma construcción. Este panorama sólo cambiará en época romana cuando los edificios públicos se construyan con ladrillo cocido, quedando el adobe relegado al uso doméstico.
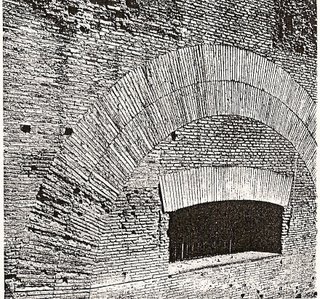
Ventana del muro meridional del Panteón
Palacio de Nippur

3.1 ARCILLA. COMPOSICIÓN, MICROESTRUCTURA, PROPIEDADES. TIPOS DE ARCILLAS.

3.2 FABRICACIÓN DE ADOBES. CONSTRUCCIÓN CON ADOBES
3.2 FABRICACIÓN DE ADOBES. CONSTRUCCIÓN CON ADOBES
Los orígenes (conocidos) del adobe se remontan al siglo VII a.C, en la región de Anatolia, en donde encontramos la ciudad de Çatalhöyük, cuyas casa ya estaban construidas con este material. Más tarde, encontramos este material en obras de gran envergadura, como las mastabas egipcias, uno de los máximos exponentes del arte funerario.
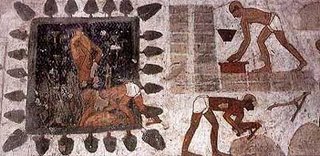
Dibujo egipcio sobre la fabricación de adobe (La vida en el Antiguo Egipto , 1994, p. 68)
El adobe se compone de arcilla(20%), arena(80%) y en algunos casos, de fibras, tanto de origen animal (crines de caballo) como vegetal (paja) que actúan a modo de “armaduras”, impidiendo la aparición de grietas en el adobe, causadas por la retracción del material al perder el agua necesaria para su fabricación, y por consiguiente, mezclando estos elementos, se crea una masa uniforme, compacta y sin grumos, que se vierte en una serie de moldes de forma prismática de madera, que recibe el nombre de “adobera” o “gradilla”. Tras este proceso, los adobes se dejan secar al Sol hasta que se evapora toda el agua, de forma que adquieren la resistencia necesaria para poder ser utilizados.
1.- Modelo de adobera para fabricar adobes medianeros.
2.- Adobe de medianería.
3.- Modelo de adobera para fabricar adobes para cerramientos externos.
4.- Ballarte: Elemento para transportar el barro.
5.-Cuezo: Elemento para recoger el barro sobrante que se empleará para realizar enlucidos.
Utensilios para fabricar adobes (Museo etnográfico-Alcubilla del Marqués)
Las medidas suelen variar, pero lo más normal es encontrar piezas de 25 ó 33 cm de longitud, 20 cm de anchura y grosor de 10 cm. Éstas dimensiones permiten que los adobes sean manejados con facilidad por el albañil, sin que sea necesaria la utilización de maquinaria, como sucede con los sillares.

Fabricación de adobe
Para su puesta en obra, existen dos métodos de utilizar el adobe:
-Puesta en obra del adobe “crudo”: antes de que la pieza de adobe se haya secado al sol, se procede a colocar el aparejo, de modo que mediante la aplicación de barro en las juntas de las piezas, se consigue “unir” los adobes, creando así un muro de mayor resistencia.
-Puesta en obra del adobe “seco”: tras haber esperado a que el Sol secase los adobes, se llevan a la obra y se realiza el apareje, tanto “a hueso” como mediante la aplicación de barro o de un mortero pobre.
Dado su proceso de fabricación, el adobe no es útil en climas húmedos, pues la arcilla que contiene es capaz de volver a absorber el agua perdida durante el secado, ocasionado un aumento de volumen de las piezas y la pérdida del material mediante la erosión por lavado, y por lo tanto, posibles daños estructurales en los edificios. Este material es un excelente aislante térmico (0,25W/mºC) lo que le hace extremadamente útil en lugares de clima cálido. Sin embargo, dada su poca resistencia, y su alta capacidad de absorción, es necesaria la utilización de otros elementos de protección, como los revocos.
Para aquellos que quieran saber más:
Construcción con tierra:
http://www.unizar.es/aeipro/finder/INGENIERIA%20CIVIL%20Y%20PLANEAMIENTO/HH06.htm
Fotografías del proceso de fabricación del adobe:
http://es.wikipedia.org/wiki/Adobe_(construcción)
Materiales del antiguo Egipto:
http://www.egiptologia.com/sociedad/materiales/materiales.htm
3.3 CONSTRUCCIÓN DEL TAPIAL.
El tapial es un antiguo sistema de construcción de muros, hecho con barro de arcilla secado al sol. Es semejante al adobe en cuanto a la composición del material (barro con algún aditivo, como paja o crin de caballo, para estabilizarlo y evitar la retracción), pero se distingue en el modo de hacer la fábrica, ya que se usan medios mecánicos: los muros se levantan por tongadas entre unos maderos que forman un encofrado.
El problema que tiene es el tiempo que necesita la preparación del barro para la fábrica, para asegurar la estabilidad de la obra una vez terminada. Habitualmente hay que preparar la masa durante meses (lo mejor es un año entero), volteándola y mojándola, antes de ponerla en obra, problema que soluciona el adobe, que puede utilizarse una vez seco.
Es una técnica muy utilizada antiguamente sobre todo en España en las actuales comunidades de Castilla y León, Comunidad de Madrid, Castilla la Mancha y algunas partes de Andalucía y Extremadura.

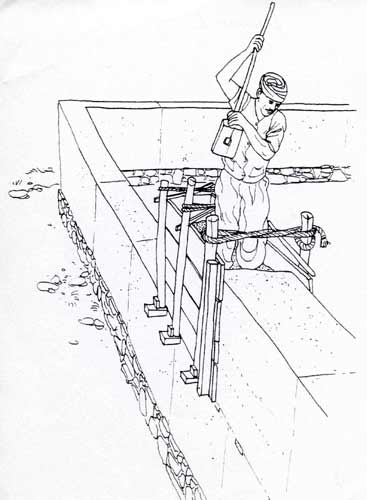


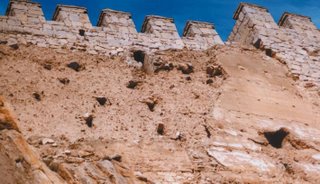

4.1 MATERIAS PRIMAS PARA LA CERÁMICA.
Los "materiales cocidos" o "cerámicos de arcilla cocida" se distinguen por tener su origen en materias primas arcillosas que se someten tras su mezcla con agua, a una conformación plástica y un proceso de secado y cocción.
Son piedras artificiales formadas por la cocción de materias primas que forman un conglomerado de materiales silíceos en una matriz arcillosa cohesionada gracias a la presencia de fundentes feldespáticos.
Son cuatro las principales materias primas de la cerámica:
De los diferentes tipos de ARCILLA, la más adecuada y utilizada para materia prima es la illita (aluminosilicato de Ca, Fe, K y Mg) por su plasticidad y su cocción a menos temperatura que otras (1100 ºC). Esta baja temperatura de cocción y el ahorre energético que conlleva, son debidos a la presencia de FUNDENTES como K2O, feldespato y los oxidos de metales. Sin embargo, también pueden aparecer IMPUREZAS calizas (caliches), yesesas, de materia orgánica u oxidos minerales (la pirita) que resultan muy perjudiciales. La arcilla también suele incluir un 30-40 % de ARENA SILÍCEA. Esto es debido a que en la industria cerámica se utilizan materias primas tales como tierras o barros que mezclan de forma natural o artificial arcillas, limos y arenas.
Dependiendo de las materias primas y de los procesos industriales seguidos, distinguiremos varios tipos de materiales cerámicos: barro crudo, cerámica porosa, cerámica impermeable, cerámica vitrificada, cerámica refractaria.
4.2. LA TRANSFORMACIÓN CERÁMICA
Redactado por Ana Oche
La ceramica es el material que aparece tras el proceso de coccion.
El proceso de coccion se desarrolla en diferentes etapas:
- 100-200 grados: el barro cocido comienza el proceso de desecacion en el que se pierde el agua que se encuentra entre las micelas. este es un proceso reversible.
- 450-600 grados. comienza el proceso de deshidratacion en el que se pierden los O y OH de la arcilla. aparece el metacaolin.
- 800-900 grados. se produce la disociacion ya que se rompe la estructura y se desarrolla entonces la transformacion ceramica. La transformacion ceramica se dice que se produce a esta temperatura porque aunque un material empieza a estar cocido apartir de unos 500 grados, no lo esta de manera uniforme, por eso el proceso por el cual sabemos que el barro esta cocido de manera uniforme es apartir de los 800 grados. En este momento ya no tenemos barro cocido tenemos ceramica. En el proceso de cocción se obtiene una cerámica porosa.
- Si seguimos cociendo el material hasta mas de 1200 grados la silice comienza a vitrificar y en ese caso tendriamos una ceramica vitrificada, que constituirá productos como el gres, semigres, klinker ceramico, gres porcelanico etc...
En cuanto a las modificaciones que se producen al transformarse el barro cocido a ceramica:
- el color pasa a ser rojizo ( por el Fe) y brillante.
- el sonido se hace mas limpio y metalico.
- el material gana resistencia y es mas resistente al agua.
- el material retrae.
- el material podra recuperar algo su expansion.
Esta es básicamente la transformacion ceramica, aunque las piezas cerámicas pueden acabarse de una manera u otra dependiendo de la finalidad que tengan. Podemos encontrar los productos cerámicos clasificados tradicionalmente en dos grupos: - la ceramica vidriada: es aquella que tiene una cara esmaltada y que generalmente recibe el nombre de loza. Se compone de un cuerpo central o "bizcocho", que es cerámica porosa, y la capa de esmalte que lo recubre por una de sus caras, dotándola de impermeabilidad. Por esta razón a veces se denomina como "cerámica impermeabilizada". Es la base de los productos de alfarería, y en construcción existen azulejos utilizados sobre todo en alicatados decorativos..
- la ceramica vitrificada: se caracteriza porque el bizcocho suele estar cocido a mas de 1200 grados,por lo que la silice ha vitrificado, y al fundirse rellena los poros dando origen a una cerámica mucho menos permeable, o que, en los casos en que la temperatura supere los 1300 ºC, pueda ser completamente compacta e impermeable. No necesitaría esmalte, por lo tanto, pero a veces lo tiene por motivos decorativos.
4.3.1 PROCESO DE FABRICACIÓN DEL LADRILLO
1. Materia prima. (Véase 4.1) Se extrae la arcilla y se transporta a la fábrica.
2. En la fabrica, se muele y se almacena, para que se homogeneice el producto y todos los ladrillos tengan las mismas características.
3. Se pulveriza y se moldea. La masa de arcilla se hace pasar por el molde y se extruye un prisma continuo que se va cortando con un hilo para dar lugar a cada ladrillo. En esta fase, el ladrillo toma su forma final, aunque no sus dimensiones finales, pues en el horno se retrae un poco.
4. Se dejan secar para eliminar un poco el agua.
5. Se meten en el horno de cocción. Es esta la fase más importante, pues es aquí cuando el ladrillo pasa de arcilla a cerámica (véase 4.2).
6. Por último, los ladrillos ya conformados y listos se almacenan en palés y se reparten a la obra.
4.3.2 EL LADRILLO Y SUS DIMENSIONES
4.3.3 TIPOS Y CLASES DE LADRILLO.


Redactado por Susana Molina
TIPOS Y CLASES DE LADRILLOS
Una posible clasificación de los ladrillo es por su uso y forma, también pos su textura o su destino.
TIPOS SEGÚN SU FORMA
Macizo: es un prisma sin huecos ni taladros. A veces pueden tener una cazoleta para el asiento del mortero de agarre. Son ladrillos prensados y se usan para muros de carga y cerramiento. Los macizos también pueden tener algún hueco pero no supera el 10% en la tabla. Se representan con una M
Perforado: tiene huecos pasantes a través de sus caras de tabla, mejorando su adherencia al mortero y colocación. Es más ligero y con iguales usos que el macizo. Se representa con un P
Hueco: es un ladrillo con huecos pasantes a través de sus caras de testa para su mayor aligeramiento. Es menos resistente que los anteriores por lo que se usa para particiones o cerramientos no estructurales. Se representa con una H. hay varios tipos según el número de huecos o las dimensiones:
Rasilla: de grueso menor a 3 cm.
Hueco Sencillo (h/s) Dispone de una sola fila de huecos. Su espesor de grueso está entre 4-5 cm. Se usa para tabiques y tableros rectos.
Hueco Doble (h/d) Tiene dos filas de huecos de 6-7 cm de grueso. Se usa para tabicones. Proporcionan mayor aislamiento acústico y facilitan la colocación de las instalaciones empotradas en ellos.
Hueco Triple (h/t) Tiene 3 filas de huecos. El grueso es igual al tizón. Tiene los mismos usos que el ladrillo de hueco doble.
De gran formato: Son los que se necesitan dos manos para su colocación, se incluyen los bloques.
CLASES de ladrillos.Se refiere a su destino:
Común (NV) Está destinado a fábricas que no dejan sus caras vistas o para revocar.
Cara vista o Visto (V) Para fábricas sin revocar.Se les exije un buen acabado estético.
4.3.4 LADRILLOS DE FORMAS ESPECIALES
Habitualmente estas piezas se emplean para:
formar parte de un arco
realizar ménsulas, encuentros en esquina, cambios de espesor y de dirección
rematar cornisas y muros
redondear esquinas, etc.
Su uso es recomendable, ya que su diseño facilita y mejora el acabado de encuentros complicados y puntos singulares.
Se deben extremar las medidas de protección, almacenaje y manipulación de estas piezas, puesto que resulta complicado reemplazarlas en caso de deterioro, además de tener un coste mayor que los ladrillos normales.
Algunas de estas piezas son:
Ladrillo abovedado o radial: ladrillo moldeado o cortado en una progresión de tamaños para formar arcos semicirculares o ventanas de ojo de buey.
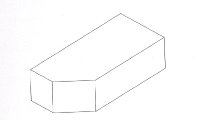
Ladrillo biselado: ladrillo especialmente modelado con una o más esquinas cortadas en diagonal. Ver imagen de la derecha.
Ladrillo cuadrado: ladrillo de planta cuadrada, es decir, no rectangular.
Ladrillo de albardilla: ladrillo especialmente modelado para su empleo en paredes de corrección, donde los cantos se proyectan para que sobresalgan de la pared con moldura de goterón para expulsar el agua de lluvia. (Ver imagen lateral)
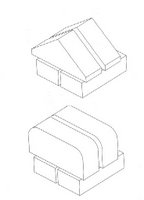
Como contraste a los de albardilla se pueden mencionar los ladrillos de corrección, que son ladrillos modelados que se colocan en los bordes al final del muro, sin que proteja los ladrillos -entonces sería un ladrillo de albardilla-. Su forma estándar es de punta redonda y albardillada.
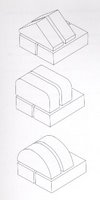
Ladrillo de zócalo: ladrillo con un corte a bisel en un lado para adaptarse a la reducción del grosor de la pared entre el zócalo que recorre la base del edificio y el muro normal de encima.
Ladrillo de caja: ladrillo terciado tres cuartos, con medio tizón cortado en diagonal para que la cara parezca aplantillada, y con el corte diagonal escondido dentro de la pared. (Imagen inferior)
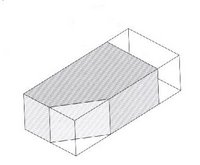
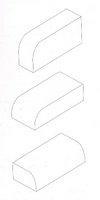
Ladrillo de esquina redonda: ladrillo que ha sido especialmente moldeado dejándole el filo semicircular en vez de afilado. Se emplea cuando una arista está dañada o para producir un efecto decorativo. (Izquierda)

Ladrillo de pata de perro: ladrillo hecho con una forma especial para que encaje en paredes de ángulos obtusos. (Abajo)
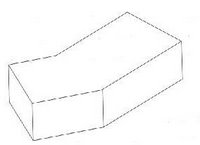
Otros: muesca, pecho paloma, etc.
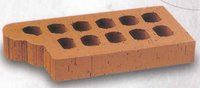
4.3.5. CARACTERÍSTICAS TÉCNICAS DE LOS LADRILLOS
Las especificaciones técnicas del ladrillo son de obligado cumplimiento en todas las obras de construcción y se refieren a aquellos que no posean ninguna dimensión mayor de 30 cm. Para ello se escogerán 6 piezas al azar, a poder ser de diferentes palés, y se procederá a su estudio.
Se pueden analizar desde dos puntos de vista:
- Tolerancia sobre el valor nominal es la diferencia entre el valor nominal de las aristas del ladrillo y el valor medio de esa.
- Tolerancia de la dispersión de las dimensiones es el valor absoluto máximo de la diferencia entre el valor medio de una dimensión del ladrillo en la muestra y cada valor aislado de la misma.
· 29 X 14 cm y gruesos de 7,5-6-5,2 cm.
· 24 X 11,5 cm y gruesos de 7-5,2-3,5 cm.
En cuanto a los ladrillos huecos se recomiendan las dimensiones siguientes, que corresponden a los tamaños de usos mas frecuentes:
Rasilla:
· 29 X 14 cm y grueso de 3 cm.
· 24 X 11,5 cm y grueso de 2,5 cm.
Hueco sencillo:
· 29 X 14 cm y grueso de 4-5 cm.
· 24 X 11,5 cm y grueso de 6-5-4 cm.
Hueco doble:
· 29 X 14 cm y grueso de 9 cm.
· 24 X 11,5 cm y grueso de 10-9-8 cm.
-Perforaciones:
- En los ladrillos macizos (M) el volumen de las perforaciones no será superior al 10 por 100 del volumen de la pieza y cada perforación tendrá una sección no superior a 2,5 cm2.
- En los ladrillos perforados (P) se habrán de cumplir las siguientes condiciones:
· tendrán, al menos, tres perforaciones.
· El volumen total de las perforaciones será superior al 10 por 100.
- En los ladrillos huecos (H) ninguna perforación tendrá una superficie mayor de 16 cm2.
-Planidad de las caras, medida sobre la soga es:
Para clase V: 2mm.
Para clase NV: 3mm.
-El espesor mínimo de las paredes de los ladrillos deberá ser:
- Pared de cara vista: 15mm (en clase V).
- Pared de cara no vista: 10mm (en clase V) o 6mm (en clase NV).
- Pared interior: 5mm.
Características físicas
La masa mínima, según dimensiones y clase:
En clase V:
Ladrillos de grueso de 3,5 cm. > 1000g
Ladrillos de grueso de 5,2 cm. > 1500g
Ladrillos de grueso de 7 cm. > 2000g
En clase NV:
Ladrillos de grueso de 5,2 cm. > 1350g
Ladrillos de grueso de 7 cm. > 1800g
La resistencia a compresión será
En tipos M y P > 100kp/cm2
En tipo H > 50kp/cm2
Los tipo V no serán heladizos.
La eflorescibilidad: los de tipo V podrán ser ligeramente eflorescidos. El ensayo de eflorescibilidad se realiza dejando el ladrillo en agua para que absorba agua por succión capilar y al evaporar se comprueba si han cristalizado sales en su superficie.
La succión será <>
La coloración será uniforme e inalterable a 600ºC en el tipo V.
Defectos de fabricación
Fisuras: se aceptará como máximo un tabiquillo partido en una muestra de 6.
Exfoliaciones: ninguna. Se producen al cristalizar el sulfato; se produce en las caras vistas de los ladrillos antiguos.
-Desconchados: se admitirá hasta una pieza por muestra con un desconchado por caliche en sus caras no perforadas con tal de que el desconchado tenga una dimensión <>
4.3.6 LEYES DE TRABA. MODULACIÓN EN LA CONSTRUCCIÓN CON LADRILLO
La trabazón de la obra de ladrillos se logra disponiendo los ladrillos en hilera solapando con los de la hilera inferior. Si la dimensión del solapado es igual a la dimensión de medio ladrillo se llama medio solapo y si es un cuarto se denomina solapo a cuartos. Un aparejo es mejor cuanto menos haya que recurrir al corte de ladrillos, pudiéndose partir de un medio o un cuarto de soga como máximo. El ladrillo se puede colocar reposando sobre cualquiera de sus caras: tabla (a soga), testa (a sardinel) y canto (a tizón). Se toma siempre como módulo el ladrillo más una junta. Al ladrillo cortado por la mitad de manera transversal se le denomina media asta.
Como norma esencial a la hora de aparejar es que dos juntas no coincidan verticalmente de lo contrario la fábrica se comportaría de manera muy heterogénea y se desplomaría al mínimo empuje. Otras reglas básicas por la que deben seguirse son:
- El aparejo debe organizarse a lo largo de la cara vista de la pared partiendo de los extremos hacia el centro.
- En la cara vista de la pared no se puede usar ningún ladrillo cortado con una dimensión menor que un tizón (exceptuando los closers que se situarán en la esquina). Esto implica a veces la necesidad de poner una pieza que mida un tizón o tres cuartos. Si se diera el caso que al replantear no cupiera un número entero de piezas habría que recurrir al “solapo roto” que se situará en el centro para no incumplir la regla primera. Como excepción está el “solapo invertido” que se aplica en trabajos de escasa importancia para no cortar ladrillos. Pero al final de cada hilada los ladrillos no se corresponden.
- Las juntas transversales horizontales deben prolongarse por todo el espesor del muro menos en las que concurran en el centro de un ladrillo colocado a soga, como se observa en el segundo dibujo.
- En el aparejo inglés si la pared tiene un número no entero de astas de espesor, cada hilada tendrá todas las sogas hacia un lado y todos los tizones hacia otro de manera alterna.
- El “ladrillo de conexión”, en una esquina, es el opuesto al “de unión”. Si la pared va hacia la derecha se necesita un ladrillo entero y uno tres cuartos dispuestos junto al “de conexión” tal como se observa en la hilada superior. En el retorno hacia la izquierda hay que colocar el “ladrillo de unión” transversalmente a la dirección del la pared como se observa en la hilada inferior.

4.3.7.1 APAREJOS TRADICIONALES
El aparejo es el término que designa la disposición ordenada de los diversos elementos pétreos, como sillares, mampuestos o ladrillos, en la construcción de muros y paredes. A lo largo de la historia se han empleado una gran variedad de aparejos, dependiendo del material utilizado, el grosor del paramento y sus cualidades ornamentales. Todos ellos, sin embargo, comparten una misma finalidad, evitar las juntas verticales continuas, que impedirían el reparto de las cargas y provocarían la aparición de peligrosas fisuras verticales.
El aparejo ha supuesto un problema dentro del proceso constructivo. La forma de resolverlo eficazmente comienza en la cultura clásica, que determinará la metodología empleada por las posteriores culturas en cuanto a la colocación del ladrillo como material cerámico.En la Grecia clásica ya se estableció un sistema de aparejos clasificados en isódomos, si todos los sillares iguales se disponían a soga; pseudoisódomos, si las piezas se componían a soga y por hiladas de distinta altura, y diatónicos, si alternaban sogas y tizones. Más tarde, Roma introdujo nuevos aparejos para caracterizar sus complejas fábricas de piedra, ladrillo y hormigón. El tratadista Vitrubio distinguió, en el siglo I a.C., entre el opus quadratum o sillería; el opus latericium o aparejo de ladrillo; el emplecton, derivado de los griegos, construido a base de compartimentos de sillería rellenos de argamasa, y el opus caementicium, compuesto por un núcleo de hormigón tosco encofrado en diversos bloques pétreos que permanecían como recubrimiento.
De esta manera en la historia de la construcción podemos encontrar distintos tipos de aparejo, que habitualmente se denominan en función de la zona geográfica en la que suelen ser utilizados. Así encontramos el aparejo inglés, en el que se alternan hiladas de tizones y sogas, dando fábrica de un pie de espesor. Este aparejo es muy utilizado para muros portantes en fachadas de ladrillo de cara vista. También se alternan hiladas de tizones e hiladas de sogas en el aparejo americano y en el aparejo belga, pero de distinta manera.



Aparejo inglés
Aparejo americano
Aparejo belga
El aparejo de tizones, o también denominado aparejo español se forma por hiladas sucesivas de tizones con un solape de medio tizón entre una y otra. Este aparejo también es utilizado como el inglés para fábricas portantes de ladrillo, su traba es peor que la del muro ingles pero su puesta en obra es más sencilla.

El aparejo flamenco se forma por sogas y tizones que se alternan en una misma hilada, y el flamenco doble alterna dos sogas y un tizón en la misma hilada. El aparejo holandés también alterna sogas y tizones en la misma hilada.


Aparejo holandés

El aparejo en panderete es el utilizado para realizar tabiques de un grueso de ladrillo de espesor y que no está preparado para absorber cargas excepto su propio peso. Una variación de este aparejo es el aparejo palomero, en el que se suprimen piezas en las distintas hiladas, y que se utiliza de forma provisional para ventilar estancias.
El aparejo a sardinel se forma por hilada vertical de ladrillos, mostrando su cara de testa.


En el aparejo de espiga la disposición del ladrillo se realiza en forma de espiga o espina.
El muro capuchino se forma por el aparejo de dos hojas aparejadas a sogas que se enjarjan con ladrillos a sardinel.
Aparejo de espiga
4.3.7.2. PUESTA EN OBRA DE LOS LADRILLOS
4.3.7.3. TIPOS DE JUNTA

TIPOS DE JUNTA
- Enrasada : alineada con los ladrillos

- Rehundida: repreta el mortero

- Matada superior: típica mudejar

4.3.7.4. DURABILIDAD DE LOS LADRILLOS
La durabilidad de los productos cerámicos es una de sus características más interesantes y apreciadas, ya que existen pocos materiales como los ladrillos que puedan resistir el paso del tiempo de una forma tan favorable y sin cuidados de mantenimiento. Sin embargo existen defectos de estos materiales principalmente producidos por la retención del agua y agentes atmosféricos que pueden afectar a la vida útil del material sino se previenen utilizando ladrillos que hayan superado el control de calidad AENOR-N y disponiéndolos de manera adecuada en obra.
Eflorescencias
Las eflorescencias son manchas producidas por la cristalización de sales solubles en la superficie del ladrillo. Normalmente se trata de un problema estético, más que de un problema de durabilidad, aunque en algunos casos si las sales son abundantes es posible que este defecto se convierta en un peligro para el ladrillo, aunque existen soluciones que dependen de los ciclos naturales de la humedad y el secado.
Las eflorescencias aparecen en la superficie del ladrillo, favorecida por la naturaleza del sistema capilar en relación con el mortero con el que se recibe. Las sales solubles pueden tener distintos orígenes empezando por los componentes como el Na, K, Mg y Ca (sulfatos), que residen en las arcillas o combustibles empleados en la cocción del ladrillo. Otro posible origen de eflorescencias es la composición del mortero debido a las cantidades de hidróxidos de sodio, potásico y cálcico, y por las adiciones que se añaden a los cementos. La gran succión capilar propia del ladrillo y el agua de la pasta pueden producir también eflorescencias.
El ensayo sobre eflorescencias consiste en hacer pasar agua a través del ladrillo , forzando la evaporación en la cara vista. Los resultados son mas desfavorables que en la realidad. Según la norma UNE67029/25 se distinguen tres tipos de eflorescencias según su intensidad:
Se recomienda para evitar las eflorescencencias: utilizar ladrillos calificados como no eflorescidos o ligeramente eflorescidos, verificar la influencia y composición del mortero utilizado, controlar la cantidad de agua del mortero, debiendo estar impermeabilizado el ladrillo si esta en contacto con la tierra para no ser afectado por las sales del terreno. Igualmente es recomendable cuidar con láminas antihumedad la ascensión capilar de agua y proteger con elementos constructivos(como aleros) la fachada de posibles filtraciones de agua, ya que cuanto menor sea la exposición de la fabrica a ésta, menos posibilidades de aparición de eflorescencias existirán.
Heladicidad
Los agentes atmosféricos, y en particular las heladas, son causantes de la degradación del ladrillo. La acción destructiva del hielo se debe al aumento de volumen (9% aprox.) que se produce al pasar el agua existente del interior del material al estado sólido durante las heladas. El hielo produce fuertes tensiones que solo pueden ser soportadas por aquellos ladrillos cuya estructura interna y resistencia sean adecuadas. Sin embargo en zonas de costa, los ladrillos deben ser no heladizos aunque no exista riesgo de heladas, ya que con la cristalización de las sales el material puede experimentar un aumento de volumen.
El ensayo de heladicidad consiste en someter al material en ciclos de hielo-deshielo, con probetas previamente saturadas de agua. La norma UNE 67028 describe el método de ensayo para ladrillos, consistente en saturar las probetas mediante su inmersión en agua durante 48 horas y ciclos de hielo-deshielo. La aparición de desconchados de dimensión media superior a 15mm o la existencia de más de una pieza fisurada, califica el ladrillo como heladizo. Aunque por la larga duración de este proceso (1 mes aprox.) se está considerando en ocasiones, que si existiera dentro de la red capilar un volumen de poros superior al 10% que pudiera quedar libre de agua, después de la saturación de la pieza, cabria esperar que el aumento del 9% del volumen del agua al transformarse en hielo, ocuparía estos espacios libres sin producir tensiones destructivas. Pero estos principios son solo teóricos, ya que no es posible establecer por el momento una relación entre el tamaño del poro, succión capilar, arcilla empleada etc...
Se sabe que los ladrillos cocidos a temperatura óptima presentan una estructura capilar más favorable a la heladicidad, que aquellos cuya cocción ha sido insuficiente. También se ha observado que a mayor velocidad de descenso de la temperatura , el agua dispone de menos tiempo para fluir por la red capilar, lo que hace que ocupe un porcentaje menor de la misma, y por lo tanto provoca la concentración de tensiones destructivas en las zonas saturadas y el daño en la pieza se producirá mas fácilmente que cuando la temperatura desciende lentamente.
Se recomienda en las zonas con riesgo de helada o ambientes marinos utilizar ladrillos que cumplan el ensayo de resistencia a la helada, evitar que la disposición de los ladrillos favorezca la saturación de los mismos y utilizar elementos constructivos como albardillas provistas de goterones, láminas antihumedad etc. Debe interrumpirse la ejecución de la fábrica en tiempo frío al ser el mortero muy sensible a la helada, no siendo efectivos los anticongelantes. Los ladrillos con absorción de agua inferior al 6% pueden emplearse en zonas de máximo riesgo, aunque no aseguran la resistencia a las heladas, ya que el valor de absorción sirve para conocer el grado de cocción del ladrillo, para un tipo de arcilla y proceso de fabricación.
Caliches
Los ”caliches” son los granos de óxido cálcico existentes en las piezas cerámicas de arcilla cocida. La expansión producida por la hidratación de estos para formar hidróxido cálcico provoca desconchados en las piezas cerámicas. Los granos de óxido cálcico se forman durante la cocción y proceden de los granos de caliza (carbonato cálcico), contenidos en la materia prima, que no han sido suficientemente triturados durante el proceso de molienda. Para tamaños menores de 0,5 mm, la actividad de los “caliches” es muy baja, siendo muy poco probable su acción rompedora. La presión ejercida por la expansión de las partículas es proporcional al cuadrado de su radio. De tal forma, una partícula de 4 mm de radio producirá un efecto 16 veces mayor que otra de 1 mm. La resistencia mecánica de la pieza es un factor muy importante para definir la vulnerabilidad de los productos de arcilla cocida frente a la acción de los caliches. De esta forma, para un mismo tamaño de caliches puede producir desperfectos en una pieza de menor resistencia mecánica que otra. La formación de tensiones es más probable si la hidratación se produce por vapor de agua ya que, si la hidratación se produce con agua líquida, la masa plástica formada puede disgregarse parcialmente y fluir por la red capilar del material sin producir tensiones.
El principal problema de este defecto es que su apreciación no es inmediata sino que su aparición varia según la humedad ambiente pudiendo darse en días, semanas o incluso meses. Es durante los meses de verano cuando el defecto suele aparecer con mayor rapidez, ya que el aire puede contener mayor cantidad de vapor y la temperatura es más elevada, lo que favorece la velocidad de la reacción. Para minimizar los desconchados por caliches, el fabricante cuenta con medios durante el proceso de fabricación como son molienda más fina, la regulación correcta de la temperatura de cocción y/o la inmersión del material en agua a la salida del horno.
El ensayo para determinar la presencia de caliches (según la norma UNE 67039) consiste en someter una muestra de 6 probetas a un baño de vapor durante 3 horas, observando a continuación la aparición o no de desconchados o roturas por caliche. La norma considera caliches aquellos desconchados cuya dimensión media es superior a 7 mm, y no se tienen en cuenta las pequeñas picaduras producidas por minúsculos granos de cal ya que carecen de importancia en el comportamiento o en la estética de la fachada.
Para la muestra sometida a ensayo el número máximo de piezas desconchadas (aquellas con más de un desconchado en sus caras no perforadas) será uno. Además, ningún desconchado de las caras no perforadas tendrá una dimensión media superior a 15 mm.
Expansión por humedad
La expansión por humedad es la característica que tienen los productos cerámicos de aumentar mínimamente sus dimensiones, como consecuencia de la fijación de agua procedente de la humedad ambiente. La expansión por humedad en los materiales cerámicos depende de varios factores, como son el tipo de arcilla, la temperatura de cocción, el tiempo desde la cocción hasta la puesta en
obra y la humedad.
El tipo de arcilla influye mucho en este tema, de manera que las expansiones de mayor magnitud se dan en piezas compuestas por arcillas de tipo caolinítico, y las de menor magnitud, en aquellas con alto contenido calcáreo.
La temperatura es otro factor importante, ya que para cada tipo de arcilla existe una temperatura de cocción para la cual la expansión es máxima, aunque esta temperatura no suele coincidir con la óptima de cocción, lo que hace muy importante el empleo de ladrillos bien cocidos.
Un tercer factor, el tiempo, permite considerar la relación expansión-tiempo como una curva de tipo exponencial observándose que una parte importante de la expansión total de la pieza se produce en los primeros días tras su cocción.
La humedad produce la aceleración de la expansión. Este efecto puede utilizarse para que la expansión del material se realice sin producir daños. Simplemente humedeciendo el ladrillo en los días anteriores a su puesta en obra se puede reducir considerablemente
su expansión residual.
Las probetas de ladrillo se ensayan introduciéndose en agua hirviendo. Dado que el fenómeno de la expansión por humedad se produce durante un periodo de tiempo largo (hay casos en los que puede durar hasta cinco años desde la fecha de fabricación) y su magnitud es muy pequeña, el método de ensayo actual se basa en provocar rápidamente el proceso para poder medir las magnitudes resultantes. Para ello se miden las probetas antes y después de someterlas a la acción del agua hirviendo. Previamente
se someten a un proceso de secado en estufa a 60 ±5°C durante 48 horas y de recocido en horno eléctrico a 600°C durante 6 horas, para conseguir regenerar el material al estado en que se encontraba a la salida del horno. Este ensayo nos da dos valores: La expansión por humedad, que indica el valor máximo de la expansión de la probeta, y la expansión potencial, que indica la expansión que de forma natural hubiera sufrido la probeta desde el momento de ensayo hasta alcanzar máxima.
Para evitar problemas debido a la expansión por humedad, se recomienda conocer los valores de la expansión por humedad del ladrillo que se va a utilizar, colocar ladrillos que lleven fabricados al menos una semana si el valor de su expansión es alto, • mantener húmedos los ladrillos hasta su puesta en obra y disponer juntas de dilatación a distancias adecuadas
Conclusión
Como hemos visto, la evitación de los problemas descritos se puede conseguir si seguimos ciertas recomendaciones en el diseño y en la puesta en obra del material, aunque las nuevas técnicas y ladrillos empleados facilitan el trabajo en obra sin que dicho material se vea afectado por condiciones ajenas como la mala colocación, la polución de las ciudades, etc.
Blibliografía:- http://www.malpesa.es/
-pdf el ladrillo cara vista y el adoquín cerámico.
Nota: Para ampliar las imagenes es posible pulsar sobre ellas para su correcta visualización.
Labels: Enrique Morales Puente, Javier Sánchez Jiménez
4.3.7.5. CONTROL DE CALIDAD DE LOS LADRILLOS
- Macizo(M): perforaciones en tabla menor 10%
- Perforado(P): perforaciones en tabla > 10%
- Hueco(H): con perforaciones en canto o testa.
-En cuanto a las clases se diferencian de dos tipos:
- Ladrillos Cara Vista(V): al menos con una cara con un buen acabado para utilizacion en revestimiento.
- Ladrillos Cara No Vista(NV): ninguna cara con buen acabado.
-Dimensiones(cm):
Se recomiendan la siguientes dimensiones según el tipo de ladrillo:
- Ladrillo Macizo(M): 29x14x7.5/6/5.2 ó 24x11.5x7/5.2/3.5
- Rasilla: 29x14x3 ó 24x11.5x2.5
- Hueco Simple(HS): 29x14x4/5 ó 24x11.5x6/5/4
- Hueco Doble(HD): 29x14x9 ó 24x11.5x10/9/8
-Perforaciones
- Macizo: A menor 2.5 cm2
- Perforado: minimo 3 perforaciones
- Hueco: A(area) menor 16cm2
-Flechas/Planeidad de Caras(mm)
V NV
> 30cm 4 6
> 25cm 3 5
> 12.5, 2 3
-Espesores Mínimos(mm)
CARA VISTA(V): 15
CARA NO VISTA(NV): 10
PAREDES INTERIORES: 5
-Masa(g)
Cara Vista(CV)
con grueso de: 35mm-------> 1000g
52mm-------> 1500g
57-70mm---> 2000g
Cara No Vista(NV)
con grueso de : 52mm-------> 1350g
70mm------> 1800g
-Resistencia Compresión:
Para su determinación se seguirá la norma UNE-67026-84, sobre 6 ladrillos tomados al azar de la muestra donde la resistencia a compresion ha de ser: 100kp/cm2 en (M y P) y 50kp/cm2 en H
-Heladicidad:
La califiación de heladizo o no heladizo se establece con el resultado del ensay segun la norma UNE 67028-84 "Ladrillos de arcilla cocida.Ensayo de heladicidad" sobre 12 ladrillos tomados al azar de la muestra dando como resultado que los ladrillos tipo V no han de ser heladizos.
-Succión: menor de 0.45g/cm2
-Coloración: uniforme a 600ºC en tipo V
-Defectos de fabricación:
- Fisuras: un máximo de 1 pieza en una muestra de 6 ladrillos.
- Ninguna exfoliación
- Desconchado por caliche, máximo 1 ladrillo por cada muestra de 6 siempre y cuando no aparezca en caras no perforadas y con diametro menor 15cm2
Por lo tanto todos los ladrillos han de pasar esta inspección técnica de control de calidad antes de ser puestos en obra, si no cumpliesen al menos dos ladrillos de la muestra de 6 de cada palé de 24 ladrillos, el palé tendría que ser reenviado a fabrica y repuesto dicho material por uno que cumpla las condiciones indicadas.
4.3.8. LA UTILIZACIÓN DE LOS PANELES CERÁMICOS EN FACHADAS TRANSVENTILADAS.
El sistema de

- Un muro interior de elevada inercia térmica.
- Una subestructura de aluminio sobre la que estará fijado el revestimiento exterior cerámico.
- Un revestimiento interior aislante sobre la fábrica de ladrillo.
- Una cámara de aire entre el revestimiento exterior y el interior.
- El revestimiento exterior cerámico.
Este sistema presenta numerosas ventajas: el ahorro energético (por la inercia térmica), la ausencia de deterioro (que dispersa la humedad y contribuye a la ausencia de eflorescencias), y la estanqueidad que evita que el agua de lluvia penetre en la camara de aire. La ventilación se hace a través de juntas horizontales que hay entre las placas y los surcos de escape se utilizan para el drenaje de agua.
Estos paneles se anclan en la fachada mediante clips, que se enganchan en tacos de aluminio.
ESQUEMAS DE VENTILACIÓN Y DRENAJE